Architectural TPMS Structures: A Prototype of Modular Energy-Efficient Data Centers
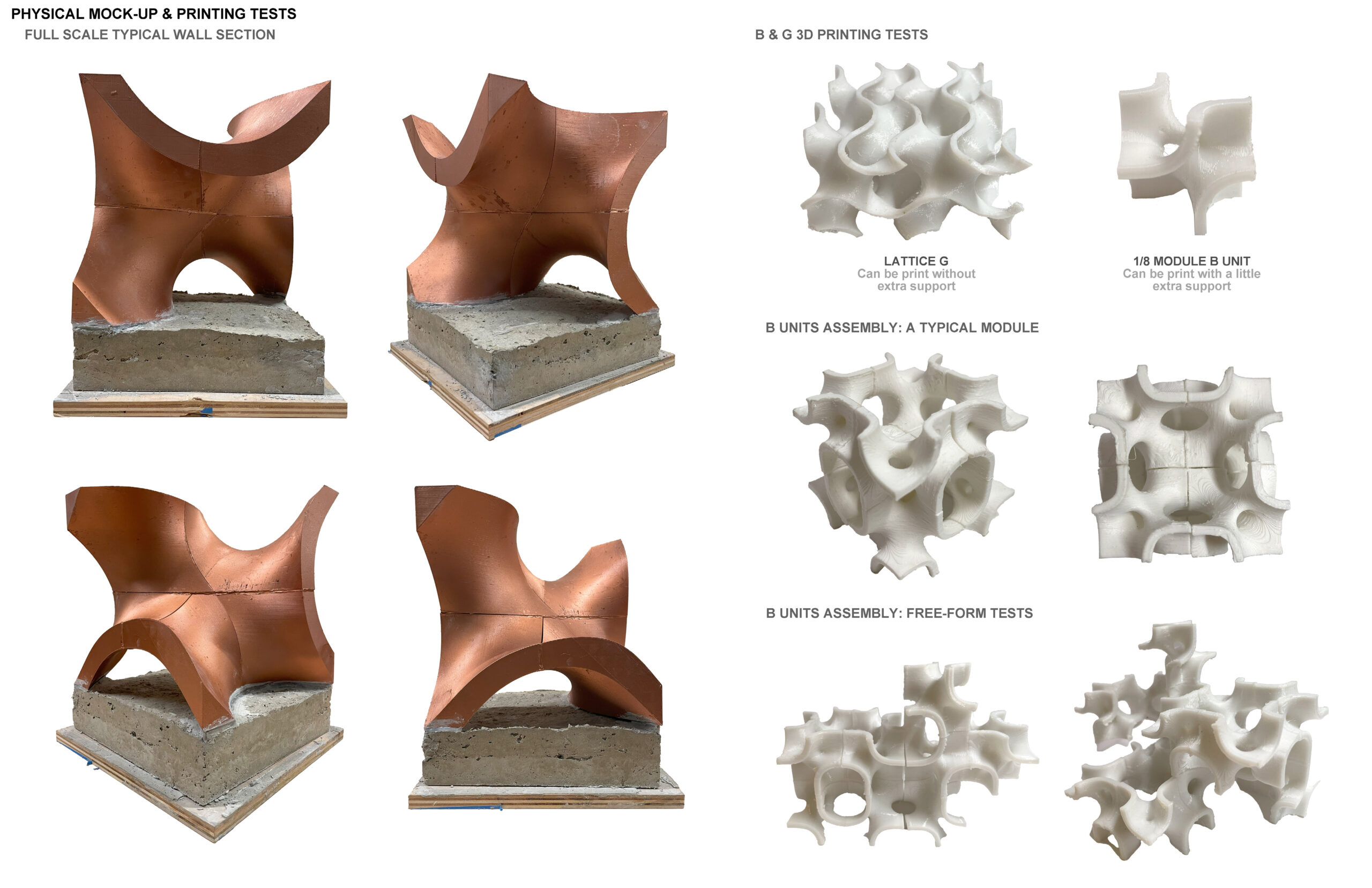
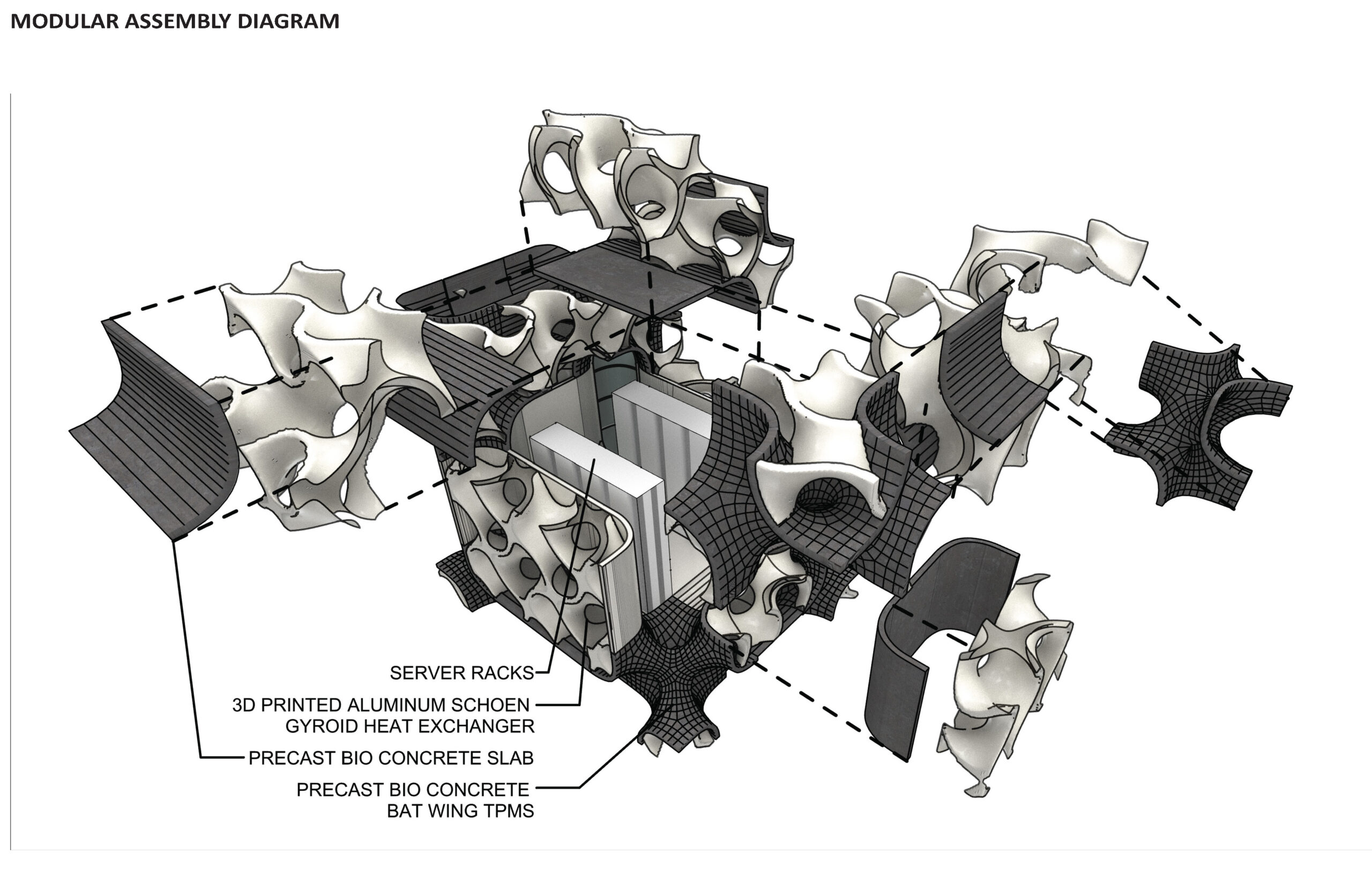
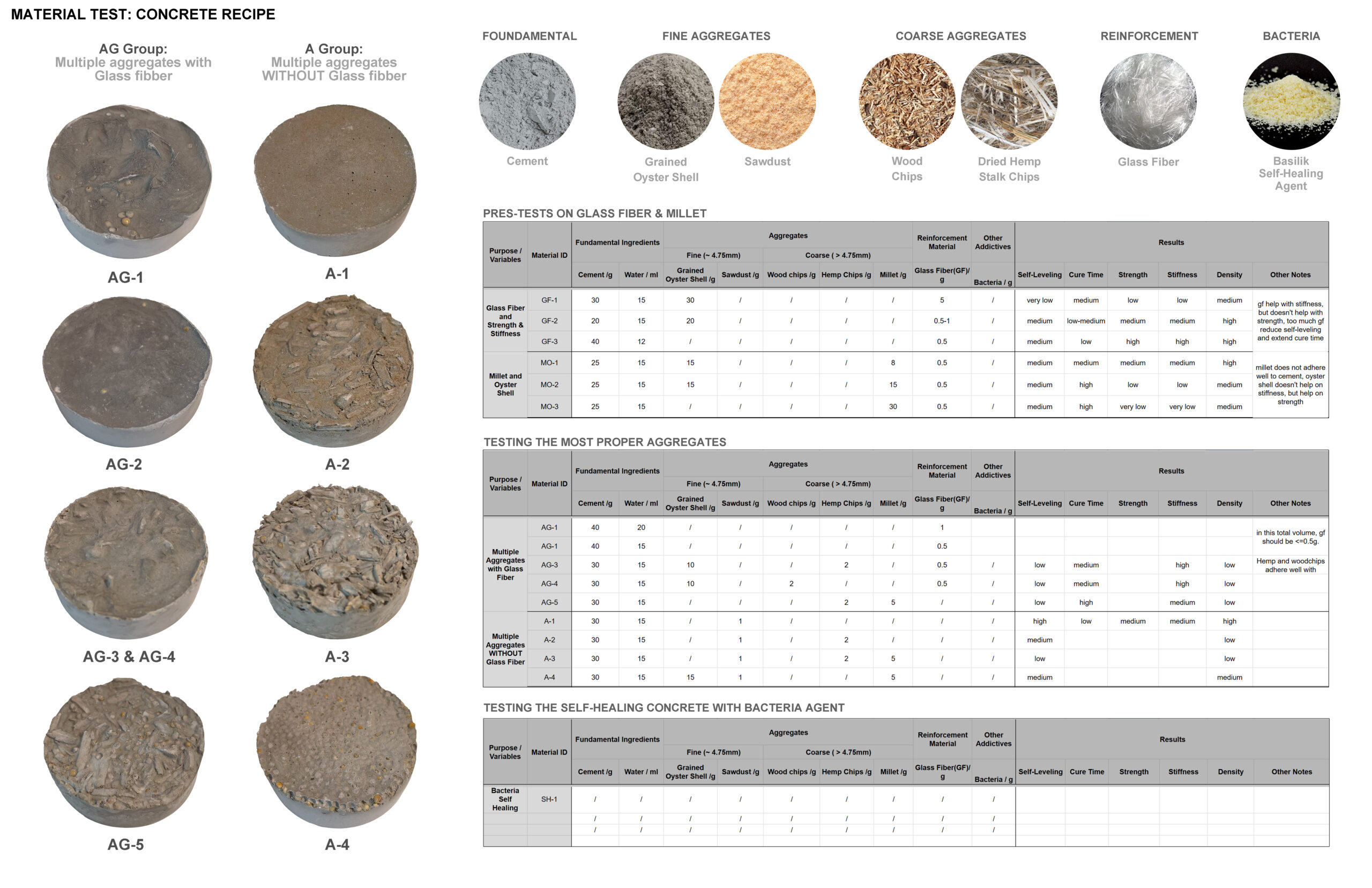
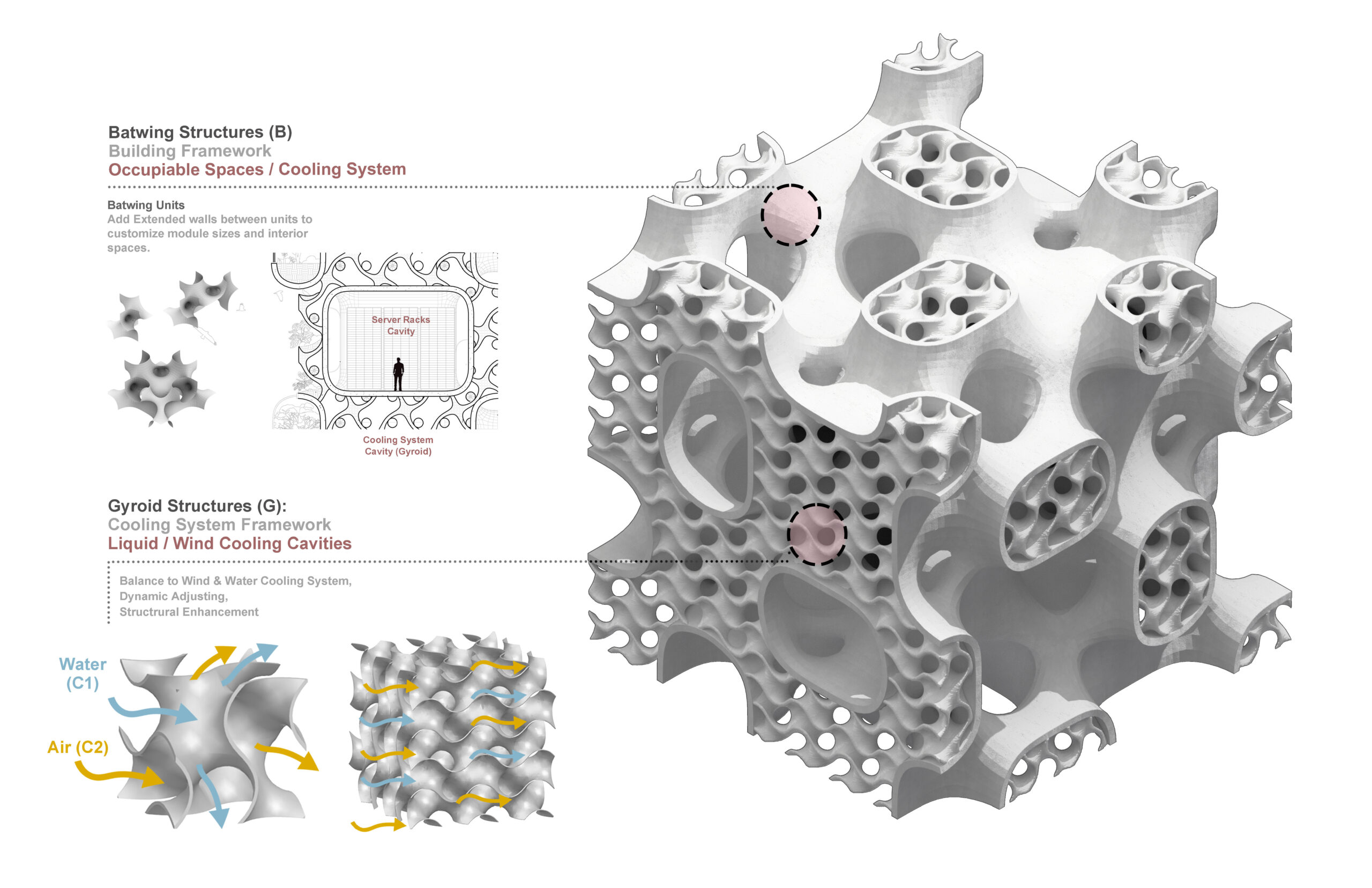
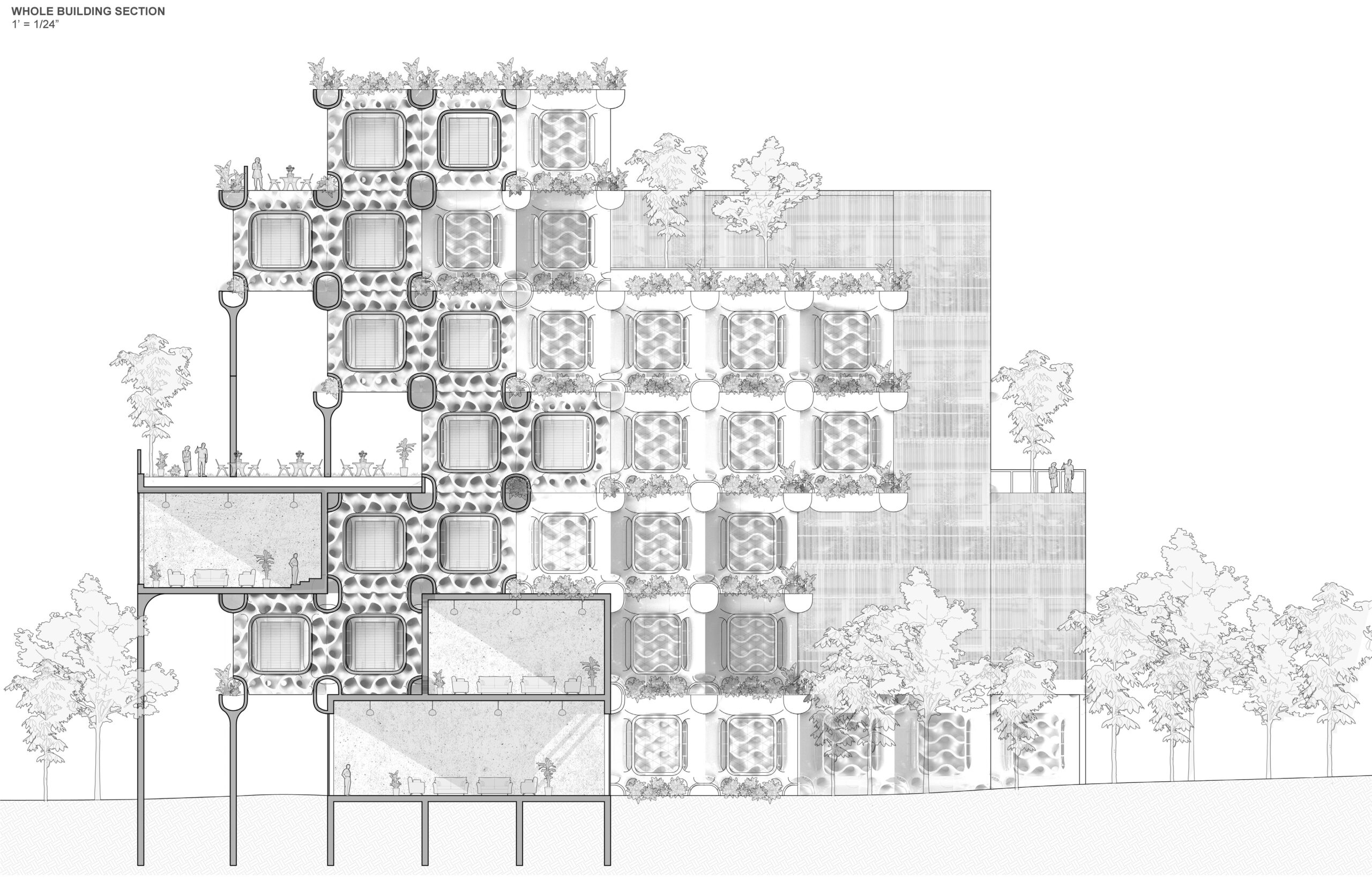
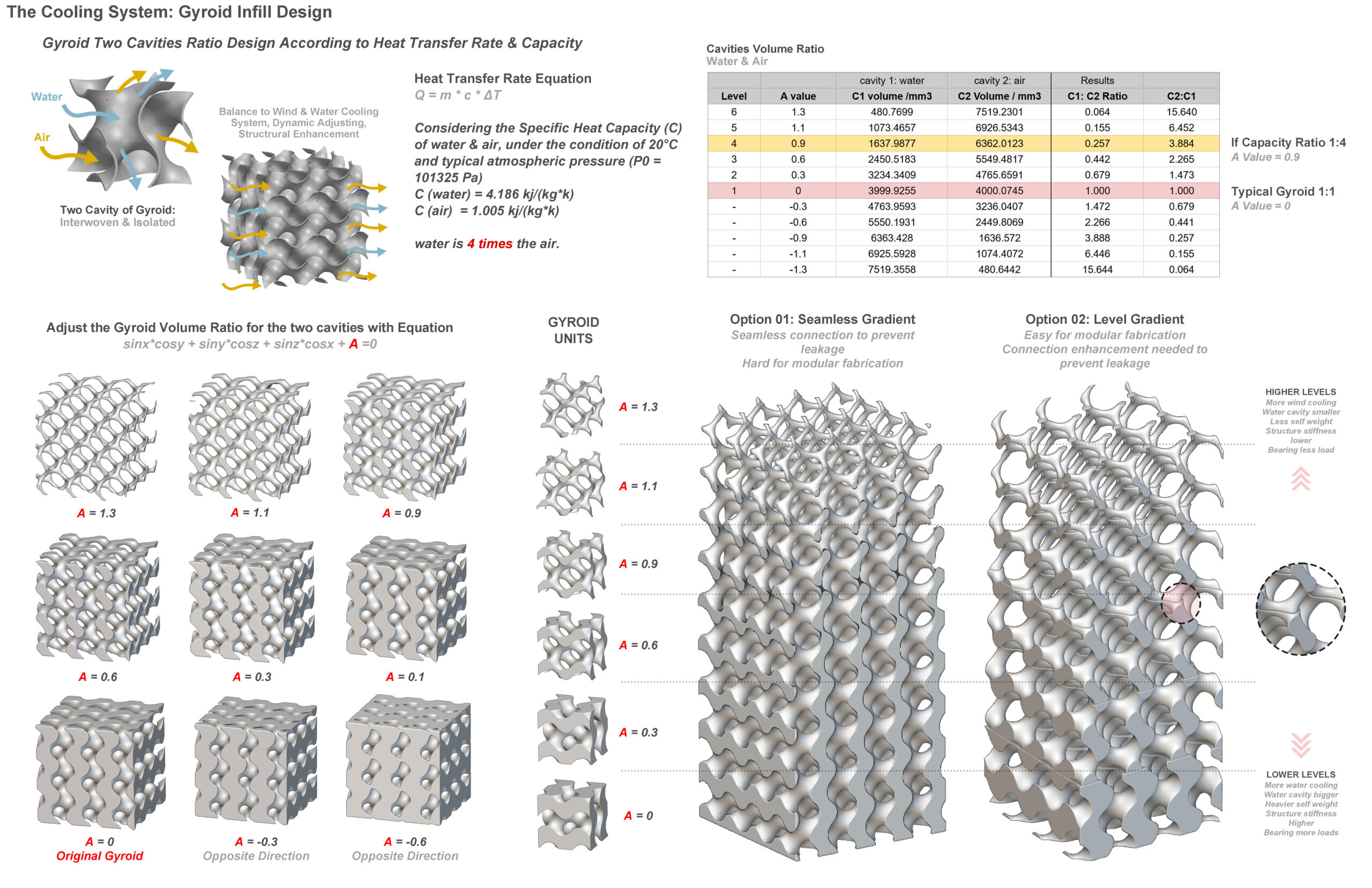
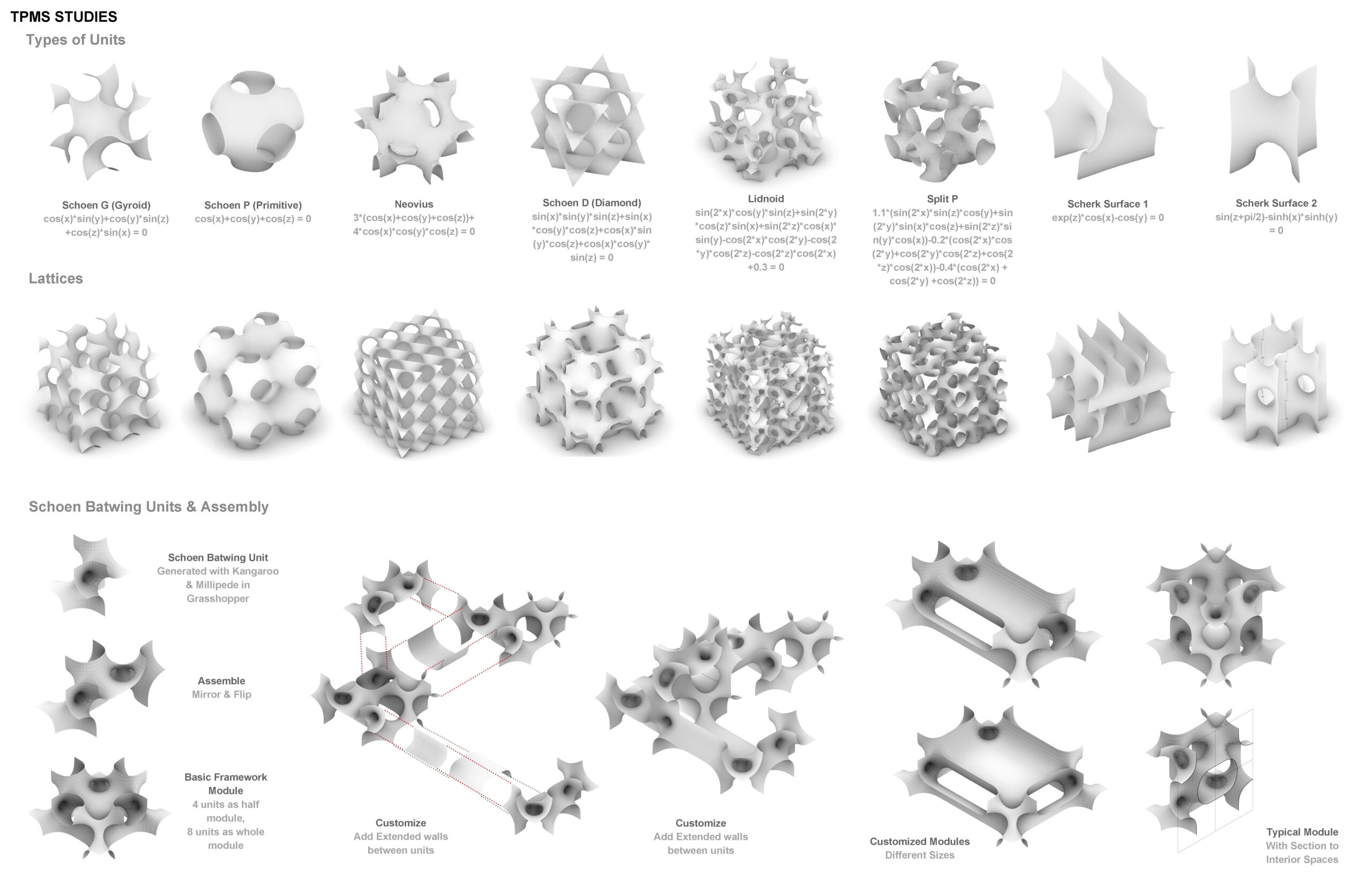
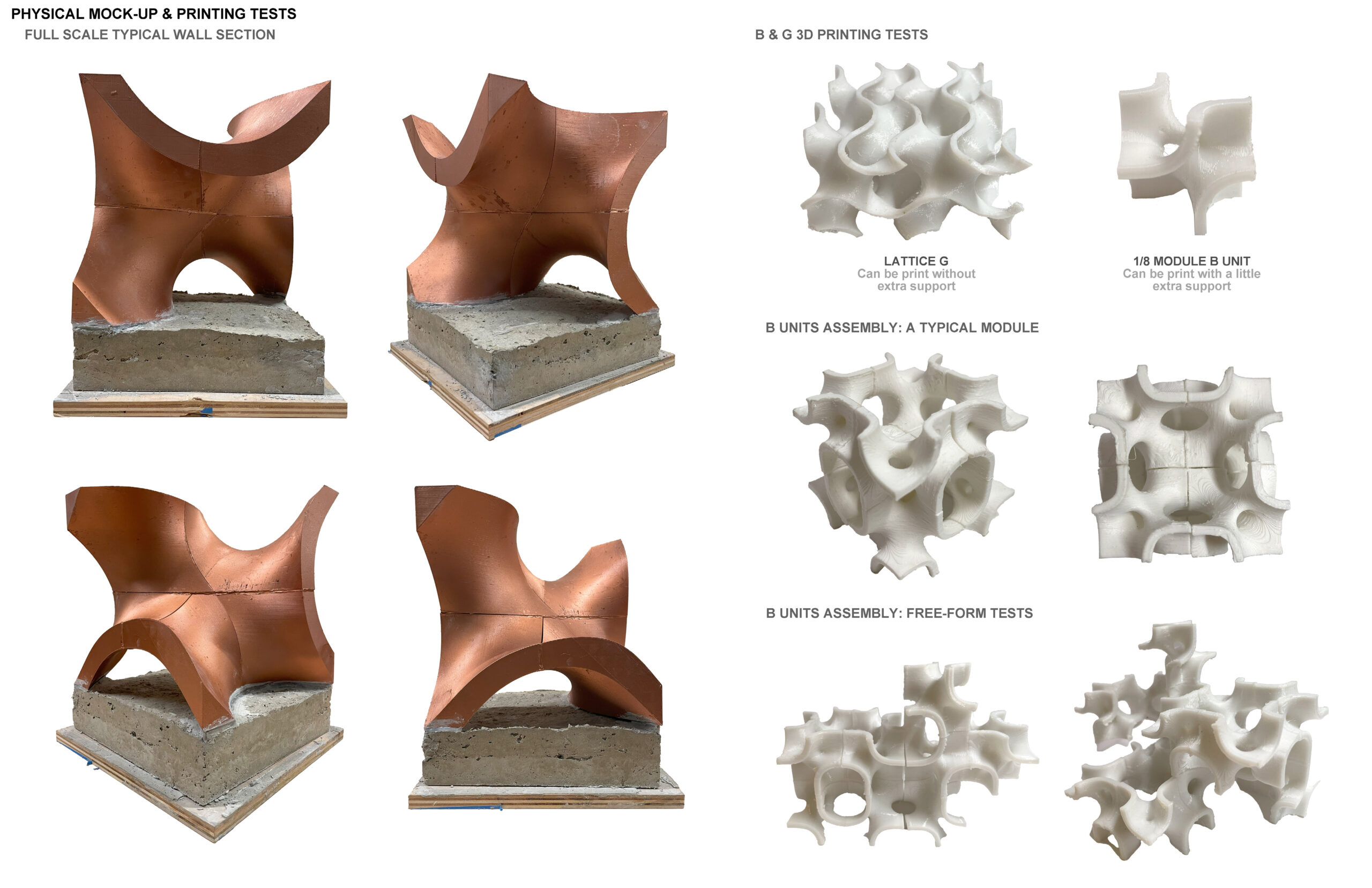
By Lucius Hu and Muzhi Wang
"In the digital age, the rising global demand for data centers highlights the critical need for more efficient cooling systems. While air cooling remains the dominant method, its high energy consumption and limited efficiency present significant challenges. Liquid cooling, which is one of the most efficient cooling methods currently used, suffers from a high cost with high risk of leakage.
This research proposes a modular data center architecture prototype that combines air and liquid cooling, leveraging the dual interwoven cavities of Triply Periodic Minimal Surface (TPMS) structures. The design integrates two scales of TPMS structures—Schoen Batwing (B) units for the building framework and Schone Gyroid (G) units for the cooling system—into a cohesive modular configuration. Key parameters, such as cavity volume ratios and wall thickness defined by TPMS surfaces, are optimized to enhance both cooling efficiency and structural performance.
Material experiments identified self-healing bio-concrete for B units and 6061 aluminum alloy for G units, ensuring durability while supporting the modular concept. This approach enables reduced carbon emissions, efficient transportation, and rapid on-site assembly. By addressing the demand for scalable, energy-efficient solutions, this prototype also facilitates energy recycling, and minimizes environmental impact, aligning with global sustainability goals."