HARESH LALVANI 2014-2015
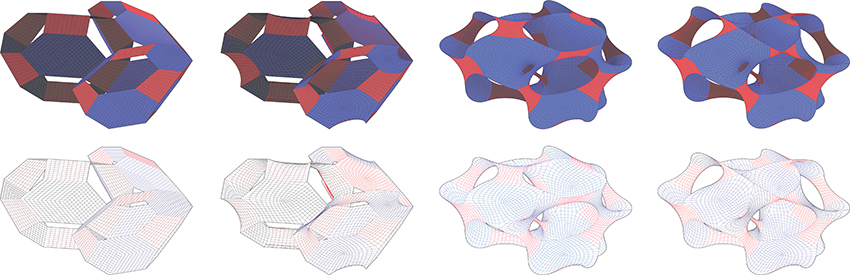
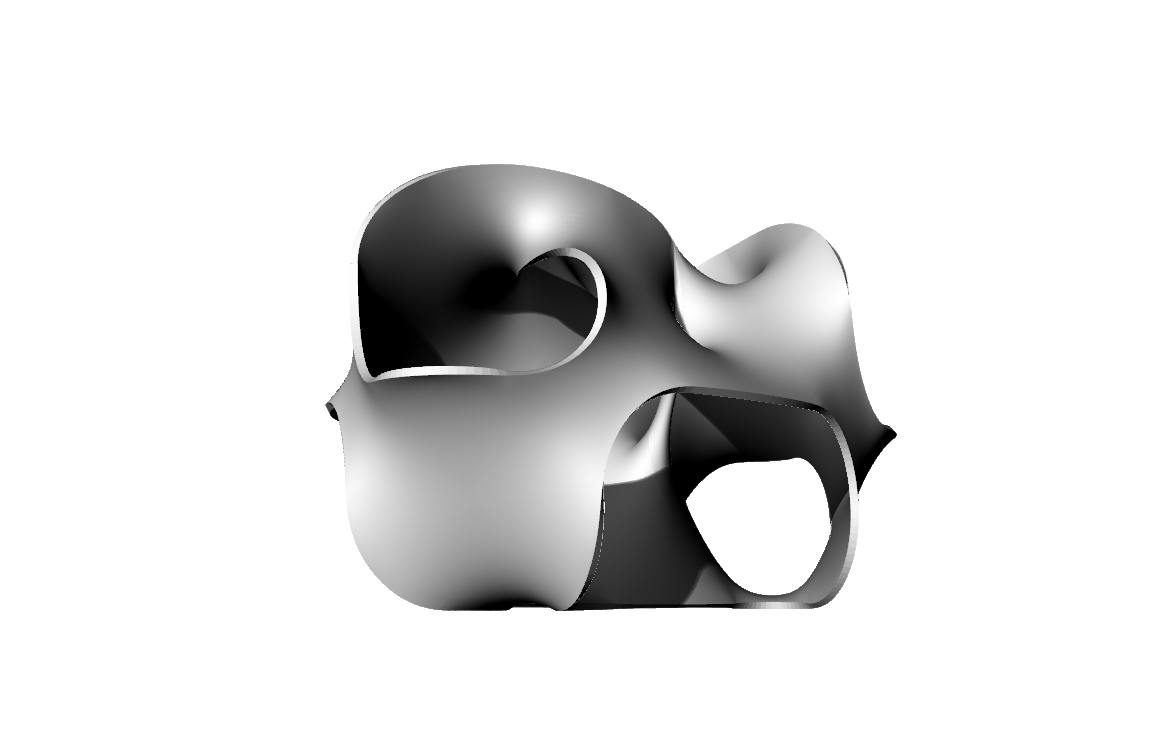
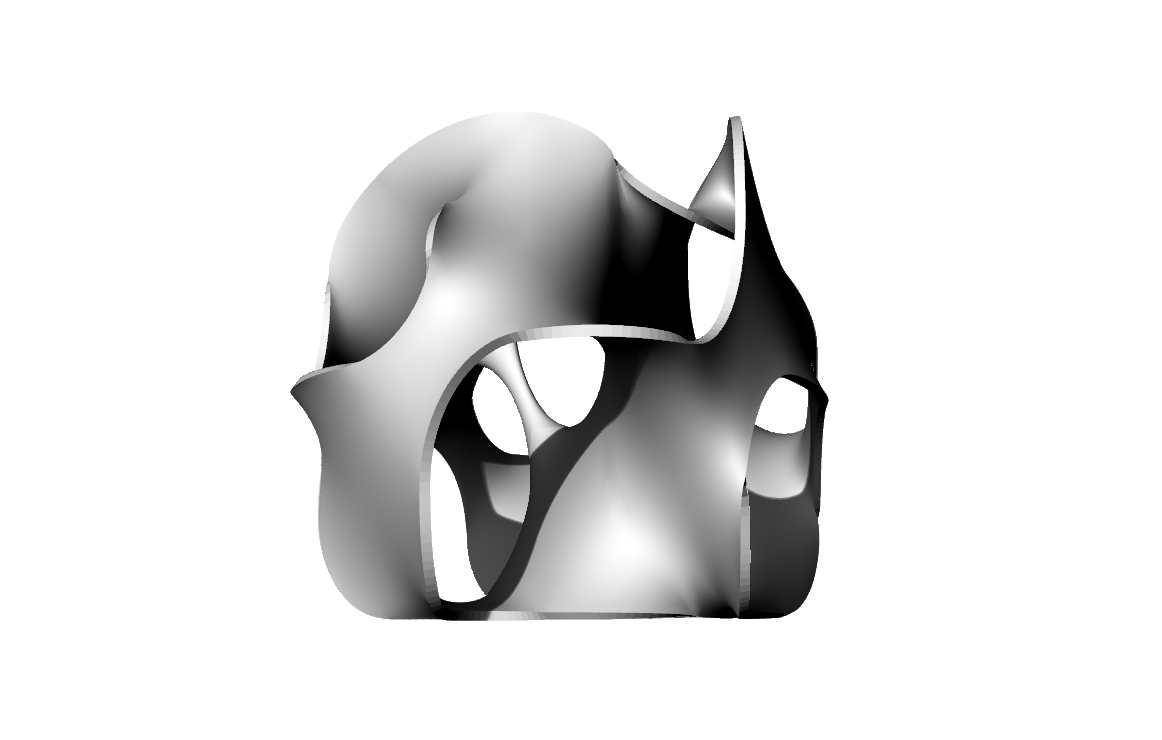
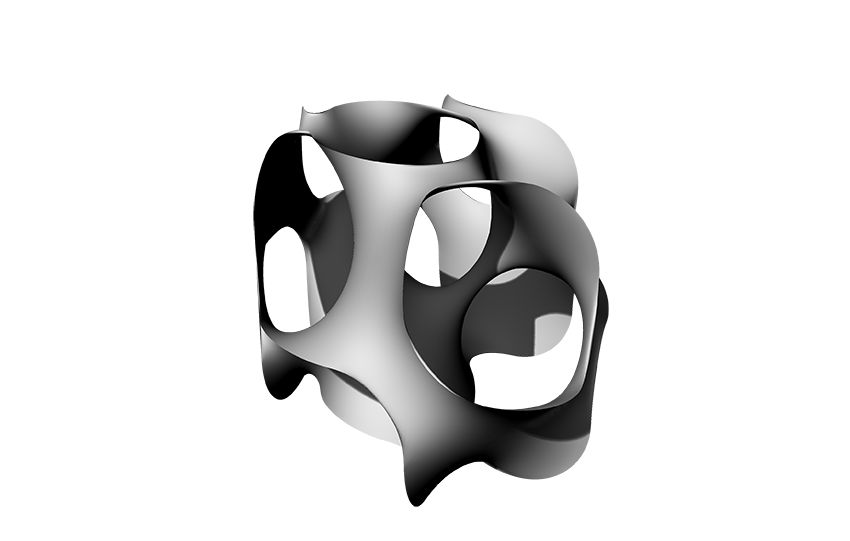
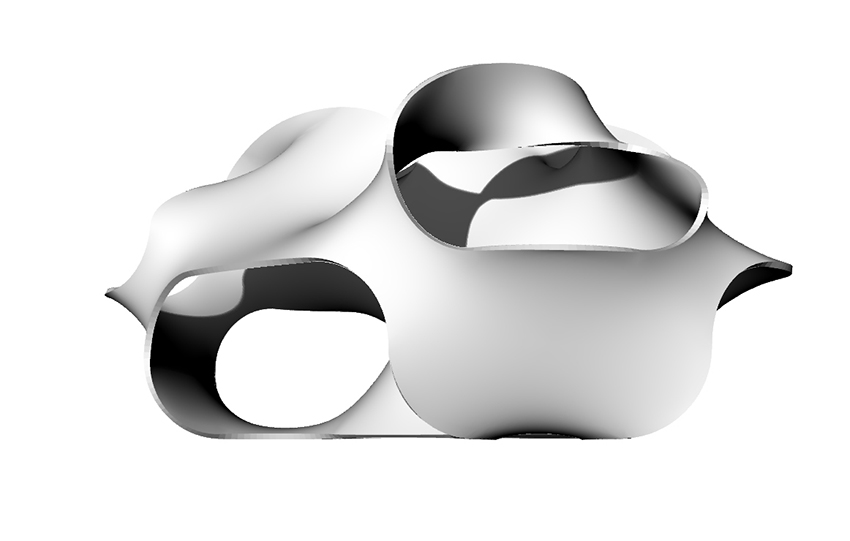
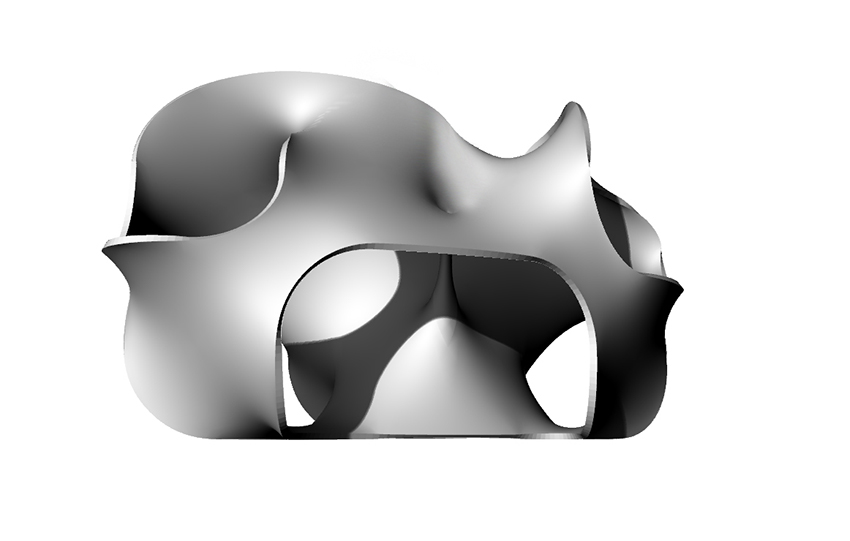
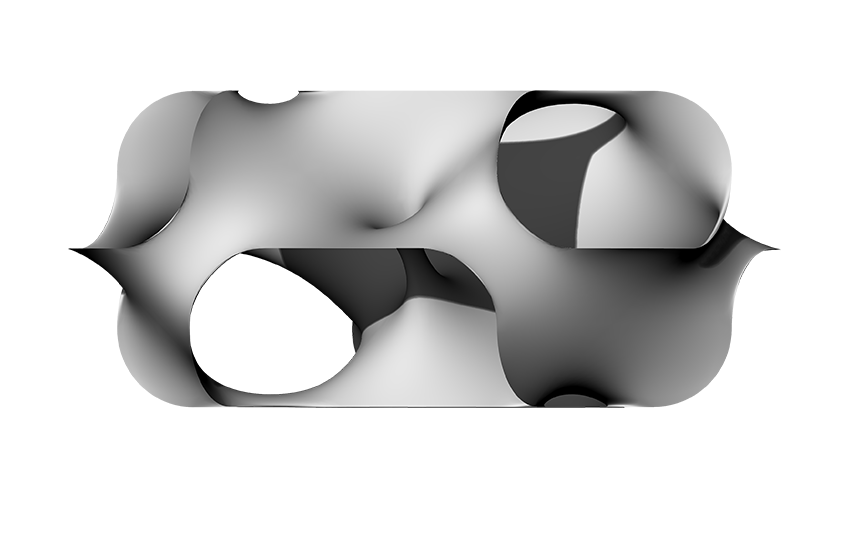
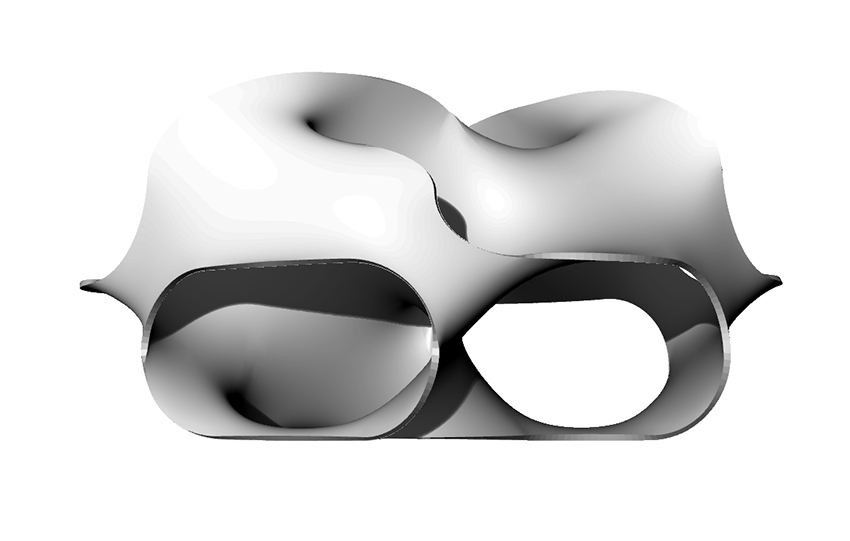
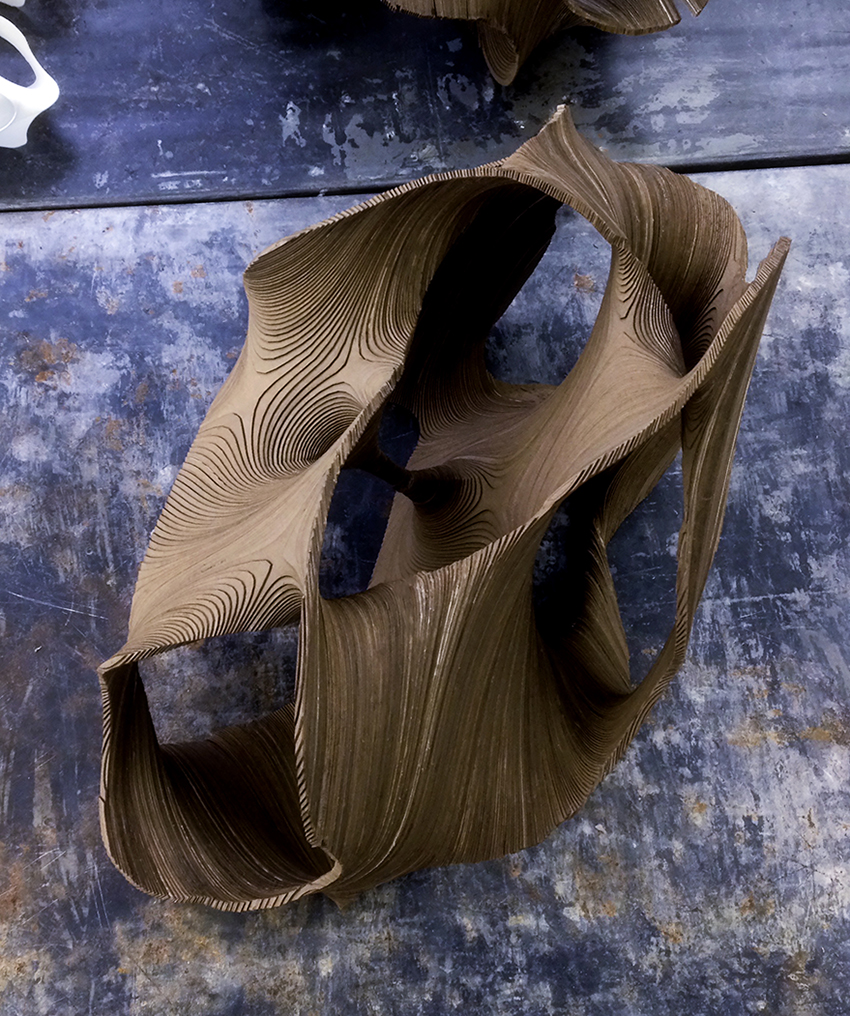
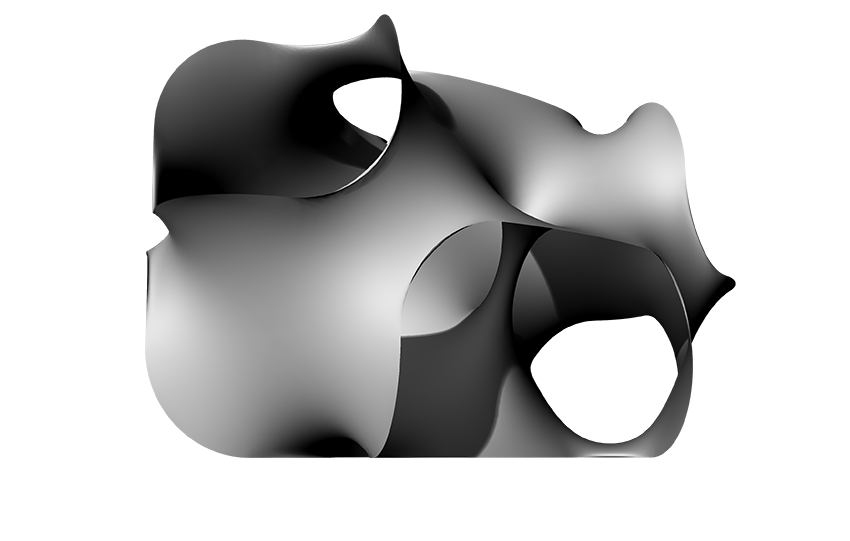
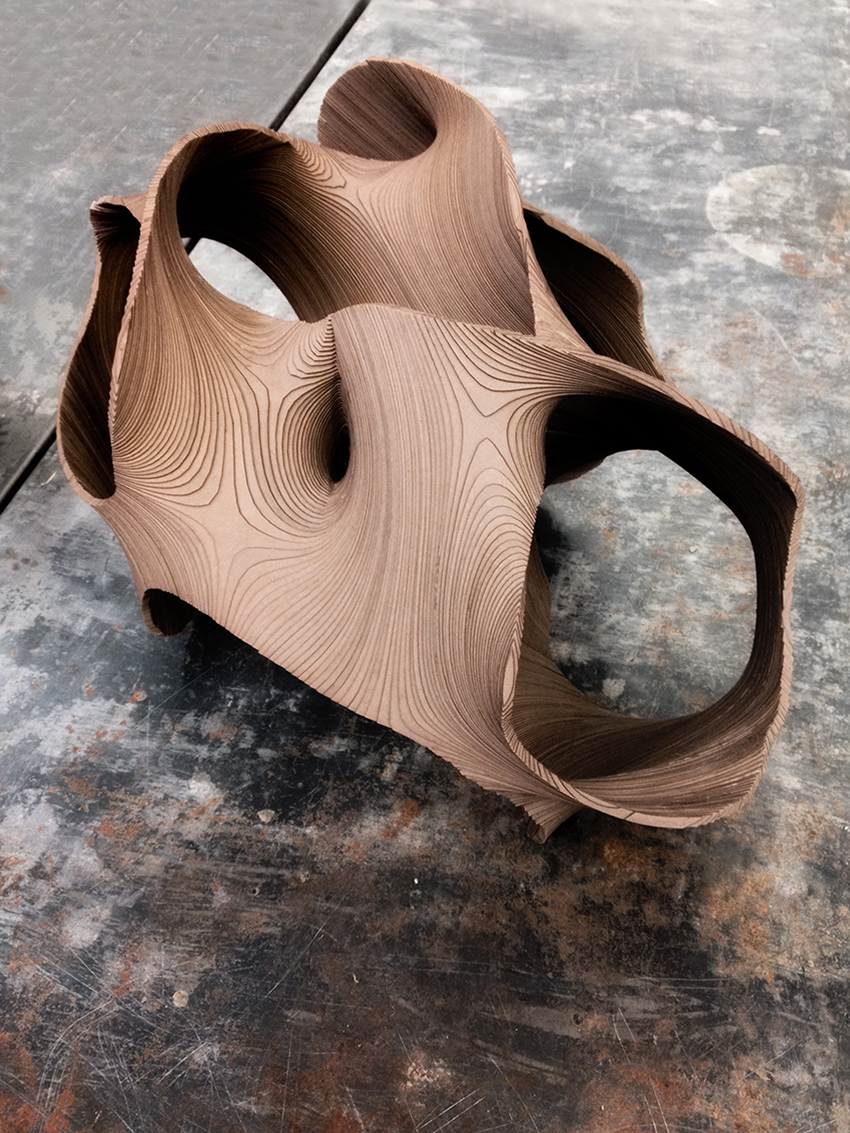
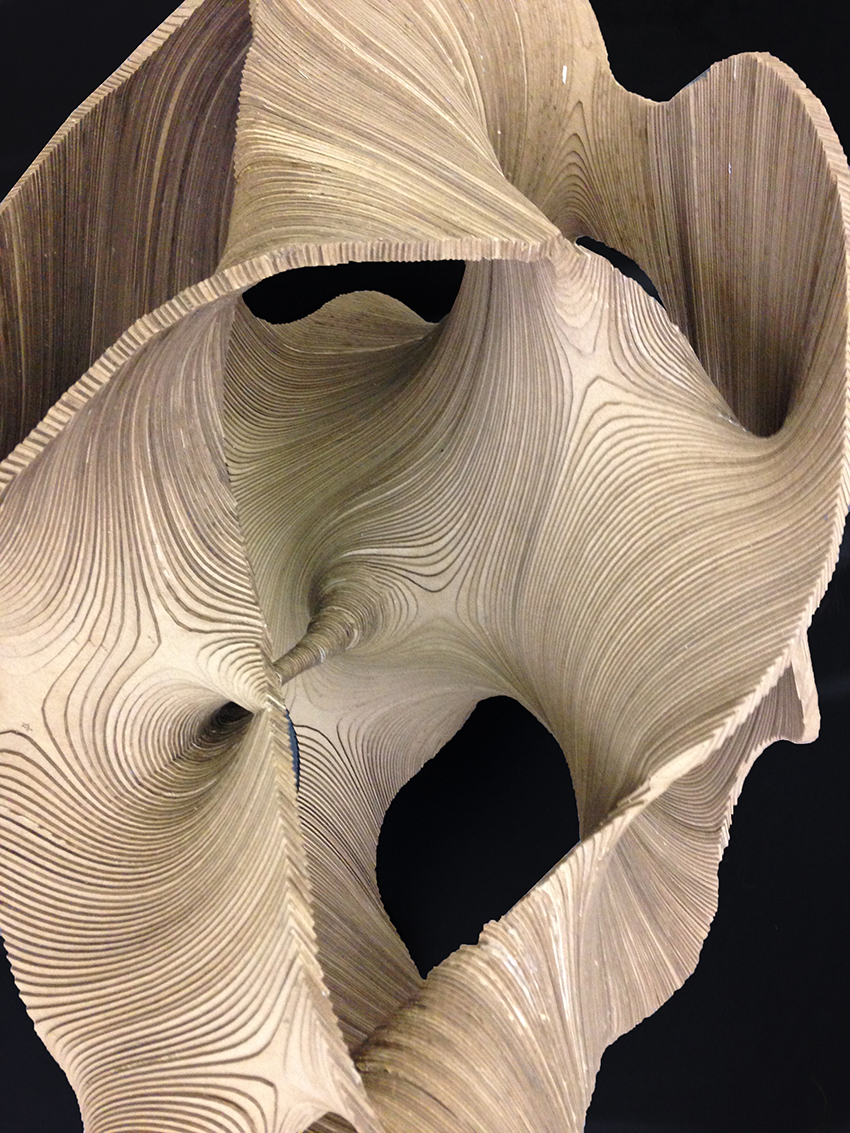
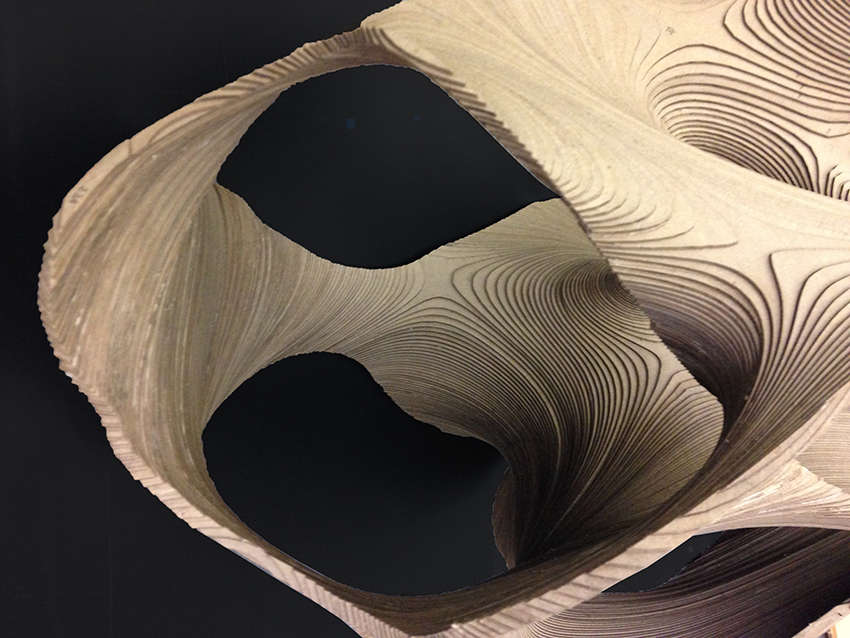
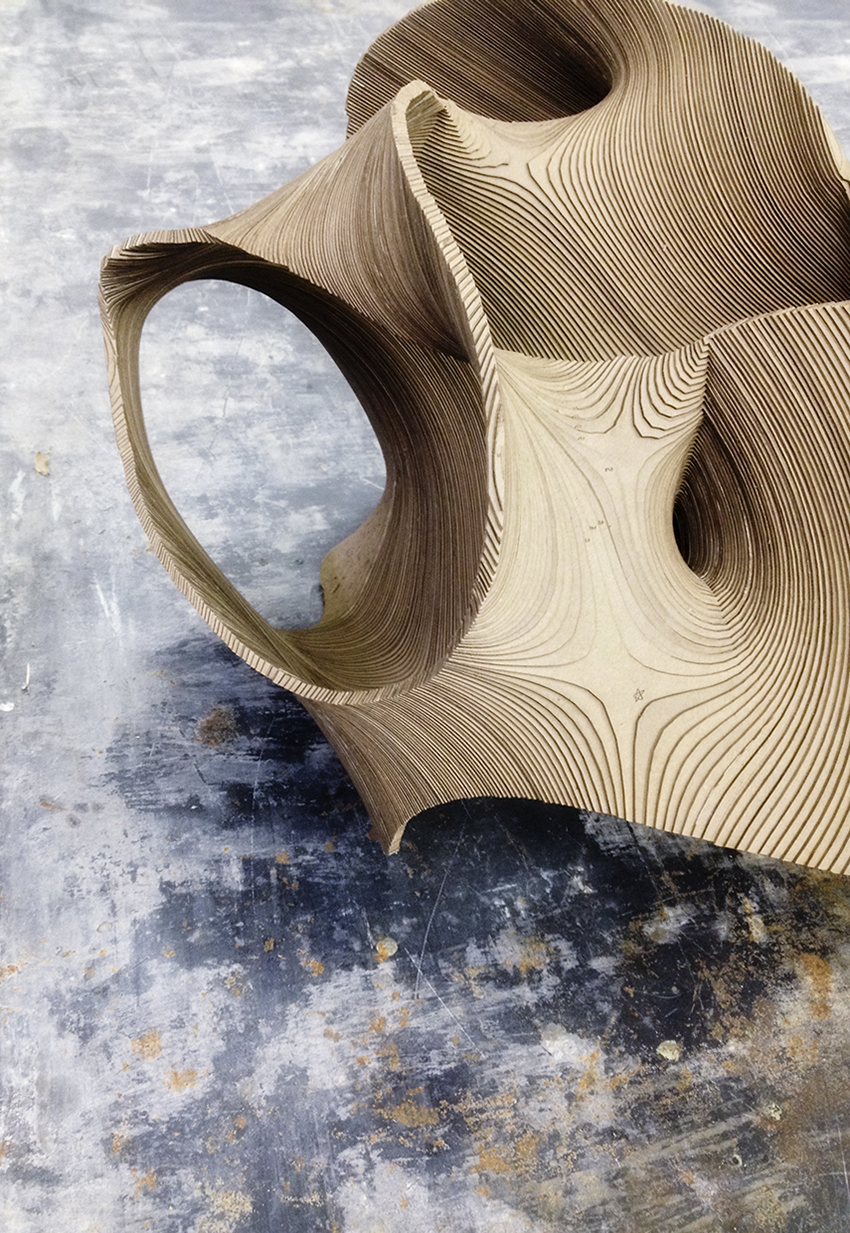
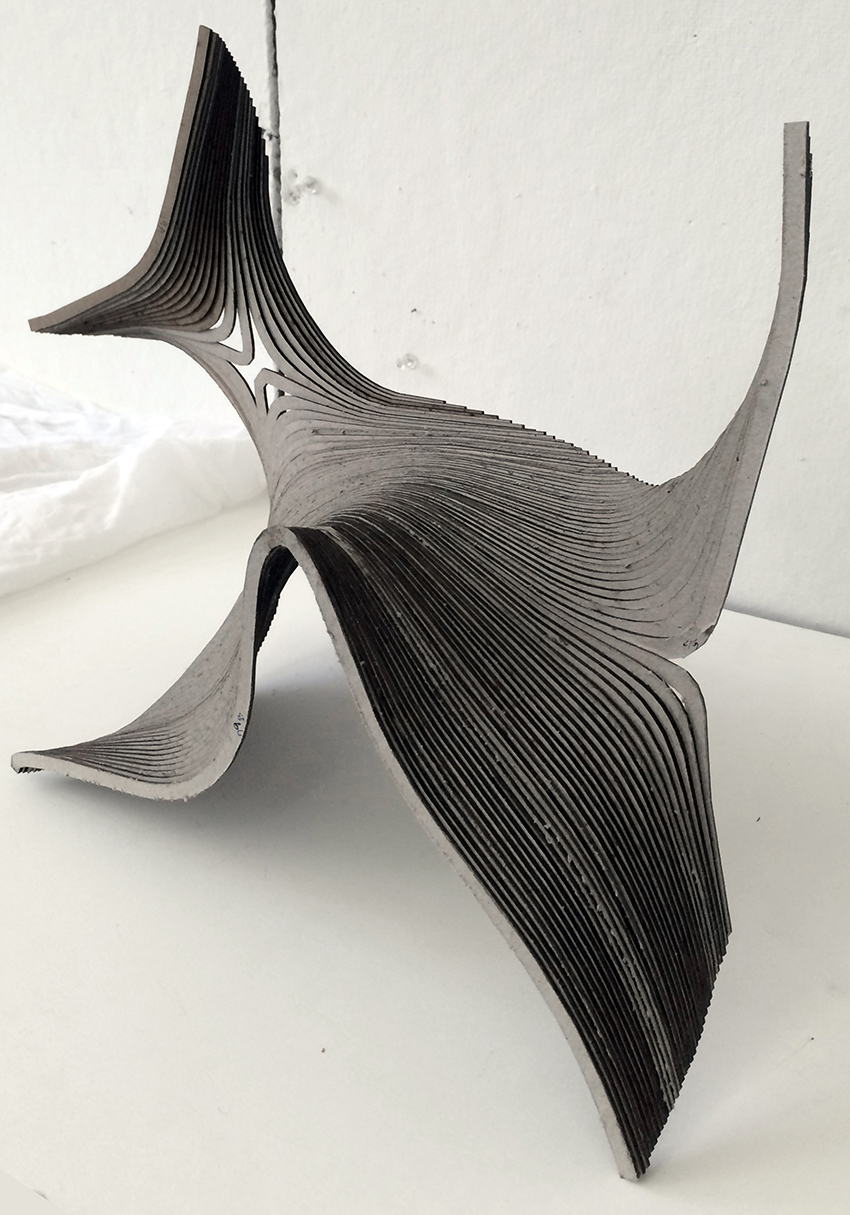
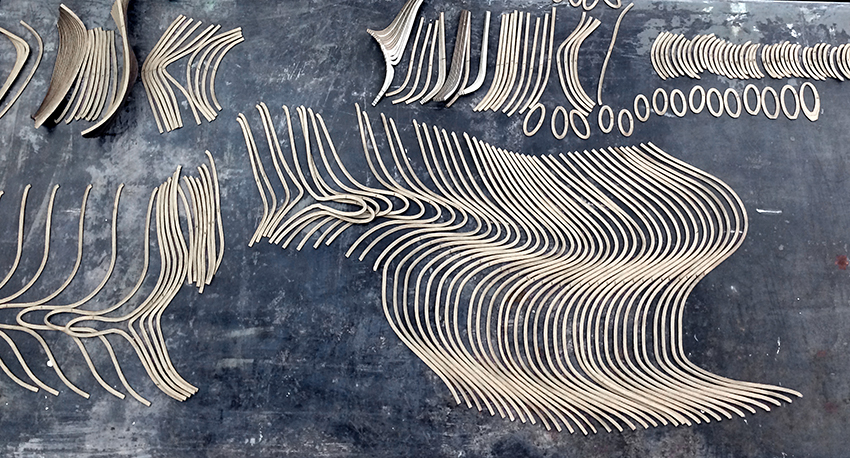
ONE-SIDED HYPER MINIMAL SURFACE
We present the first example of a one-sided minimal surface embedded in higher-dimensional space (n+1 dimensions) and projected in 3-dimensions. Its “plan” is a 2-dimensional projection of a cubic lattice of dimension n, +1 is the “vertical” dimension. This provides the starting point for development of a new outdoor experimental structure for OMI Architecture, Ghent, NY. At OMI’s request, the project was initiated at Lalvani Studio (1-10), and developed with Pratt students (11-17). This multi-semester project is expected to be completed in June 2017. We present progress from earlier semesters starting Fall 2014.
Form (1-10): Top two rows of images (1,2) show sequence of development of the one-sided minimal surface (d) from basic source geometry (a) comprising 3 cells, each with red and blue polygons. The bounding boxes of these cells are deformed cubes. The edges and faces of cells are curved in (b) and tensed into a minimal surface in (c) leading to the topological emergence of an interior (red) column. The upper red polygons are twisted in (d) to obtain a one-sided minimal surface, a complex 3d version of the Mobius strip.
The images that follow (3-10) show the architectonic quality of the form and spaces obtained this way. Images show different views of the starting surface and the derivative one-sided minimal surface.
Development/Production (11-17): Since alucobond, a rigid sheet material, was available for building, the challenge was to build a complex surface from flat sheets. This led to a laminated shell structure built from layered and contoured strips to achieve a monocoq shell construction from flat rigid parts. Images show the first iteration of this building system fabricated from 1/16” thick laser-cut chipboard strips. Automated procedures for generating strips at variable inclinations along with indices for assembly were developed. The images show a fully assembled maquette and parts/strips before assembly. Currently, we are refining the production method, scaling up the system and developing sub-assemblies to facilitate full-scale production in alucobond with industry partner Milgo-Bufkin.
Digital Expert: Patrick Donbeck
Rendering (right page): Anna Oldakowski
Students (Production/Development): Hayden Minick, Charlene Leung, Hilary Flannery, Zherui Wang, Ardon Lee, Anna Aoldowski, Diane Juarez, Vincent Zheng.