HARESH LALVANI 2015-2016
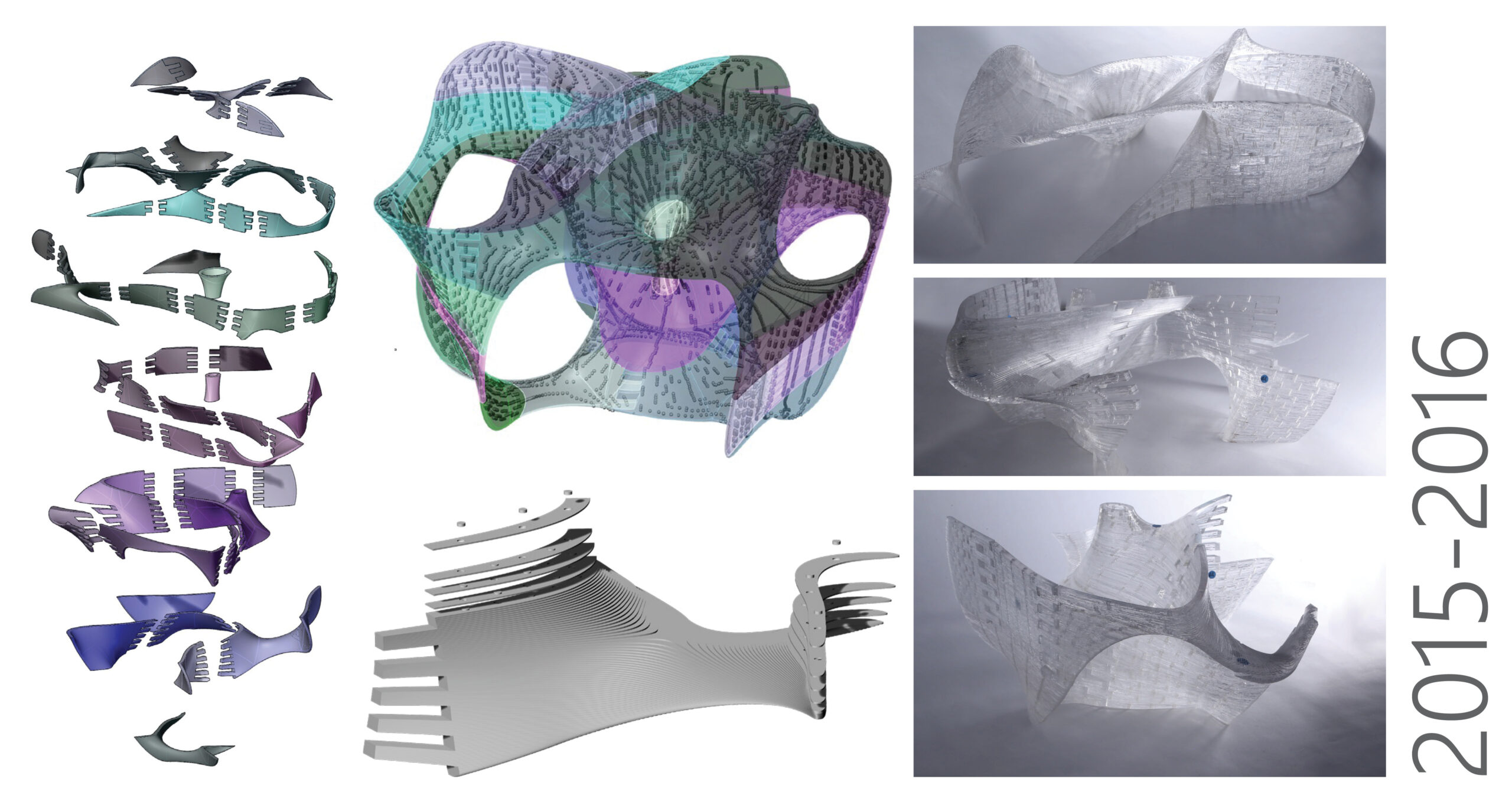
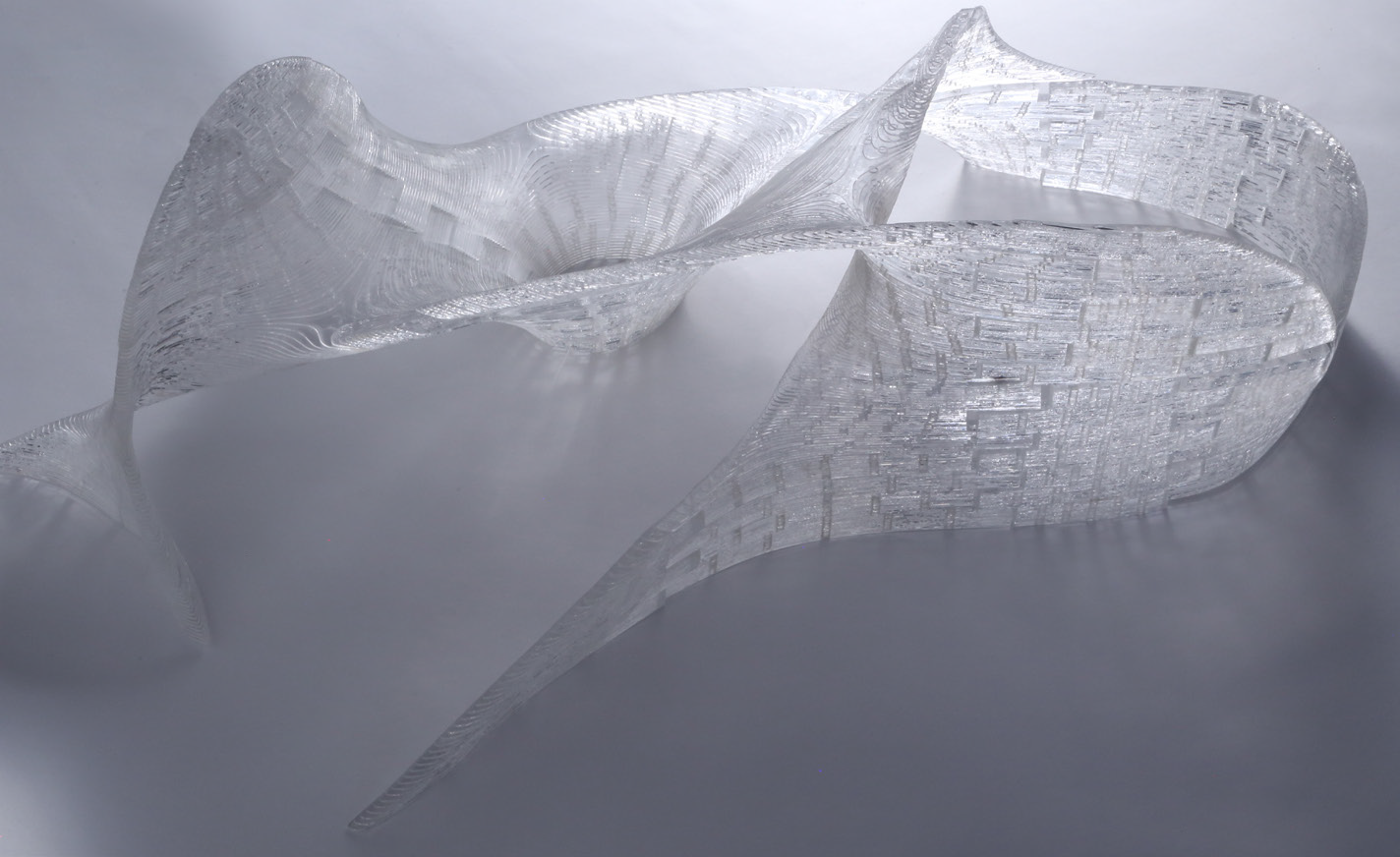
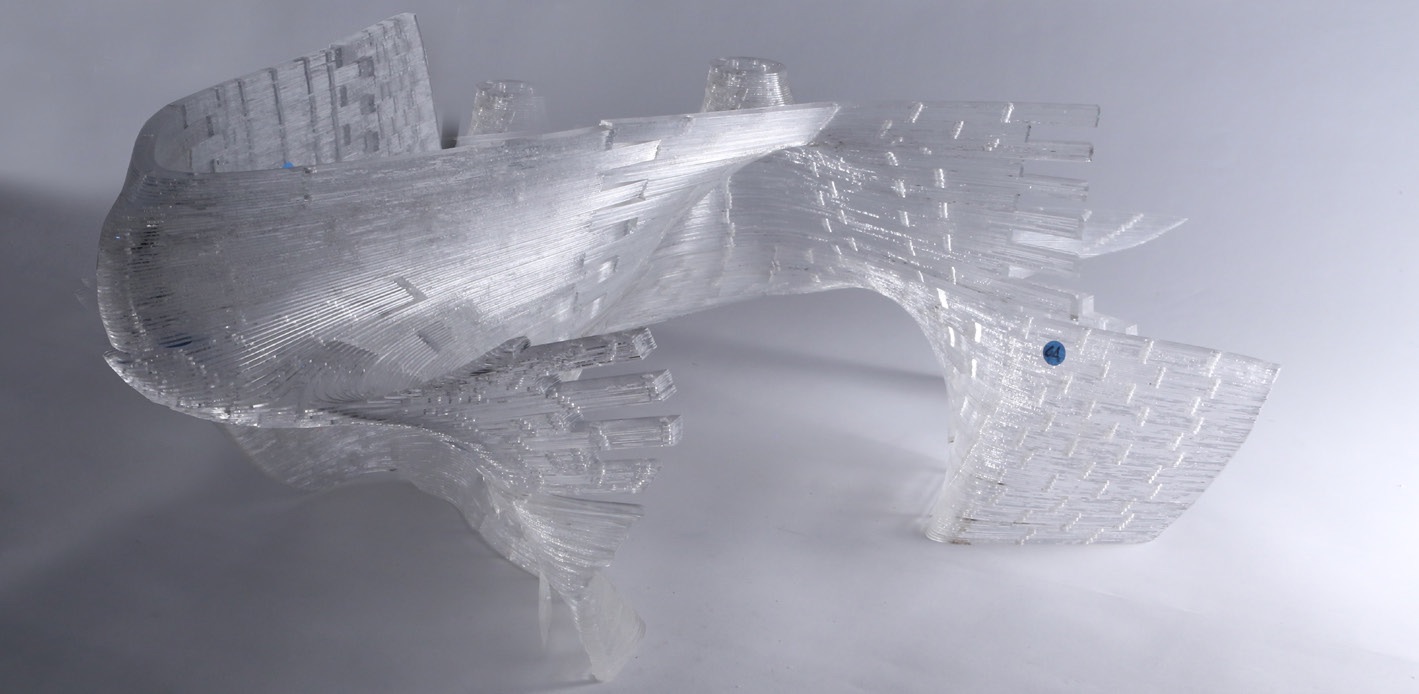
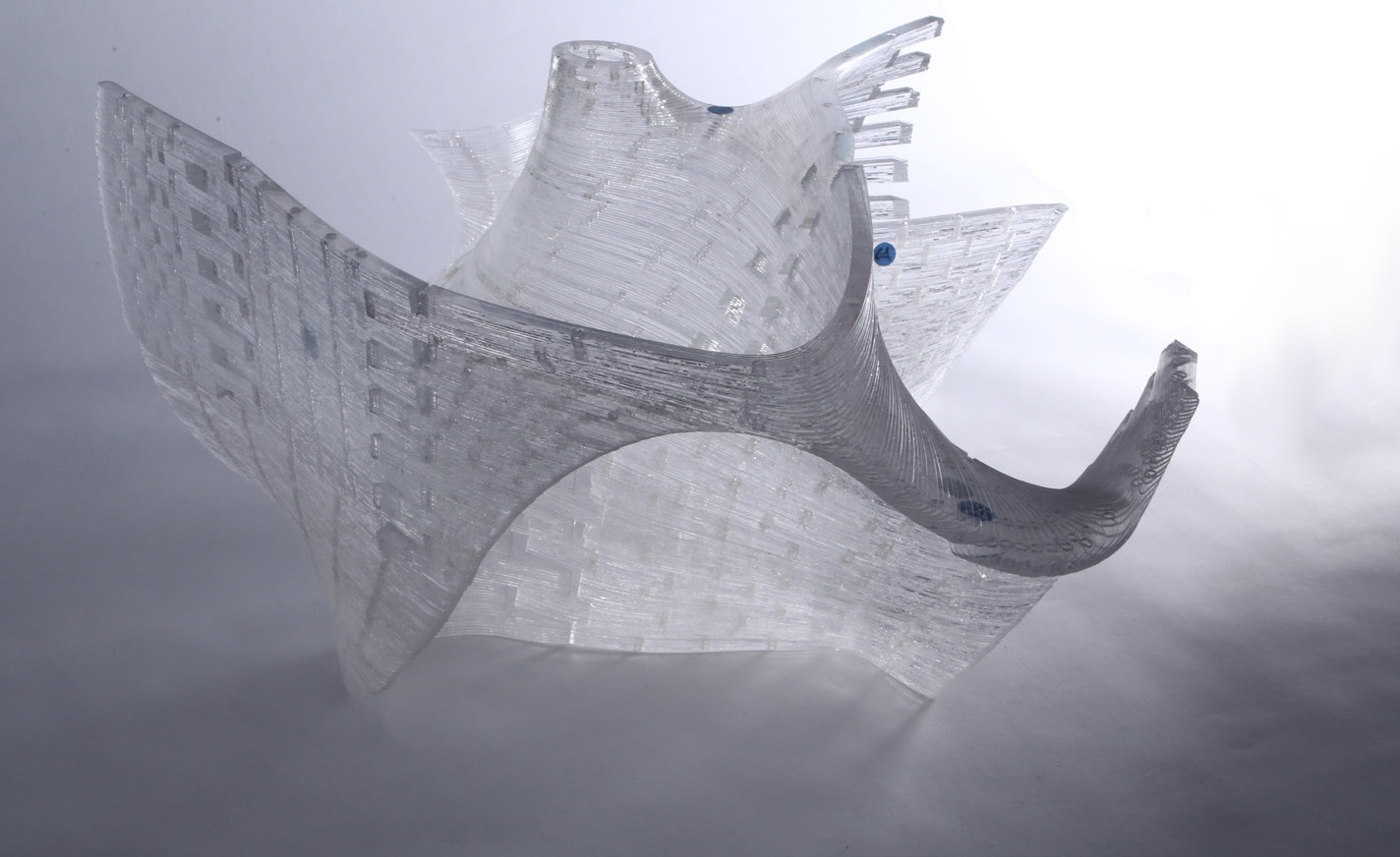
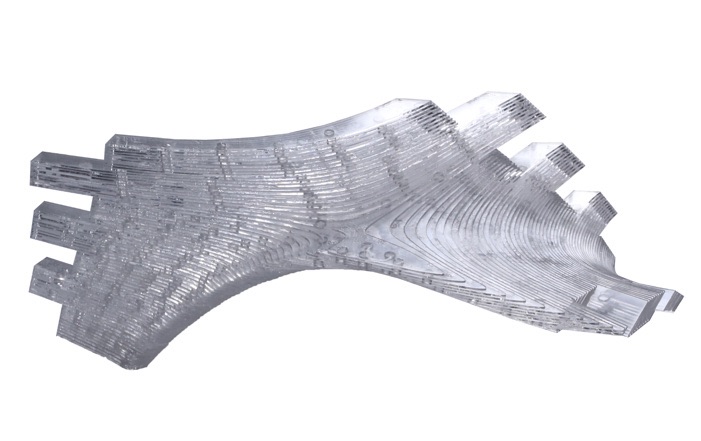
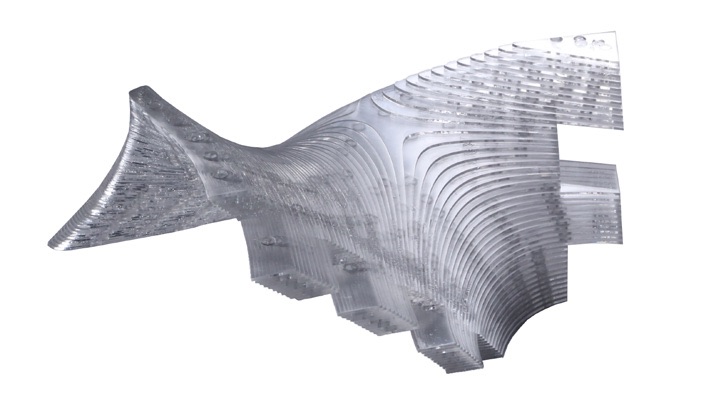
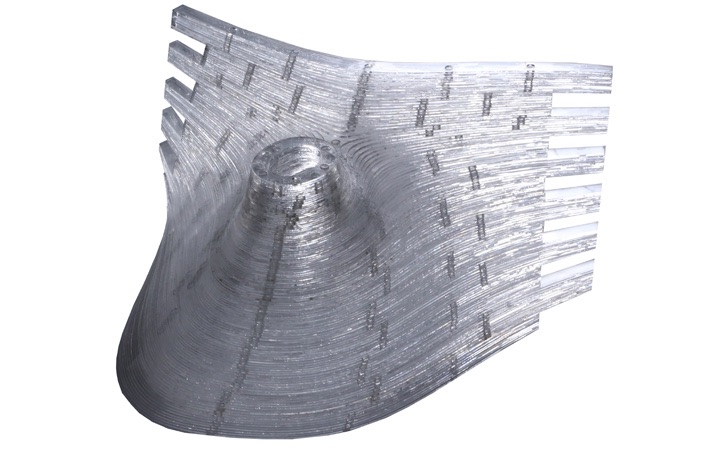
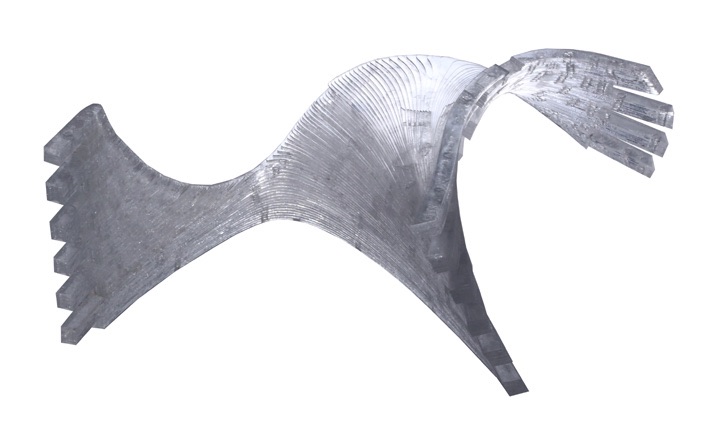
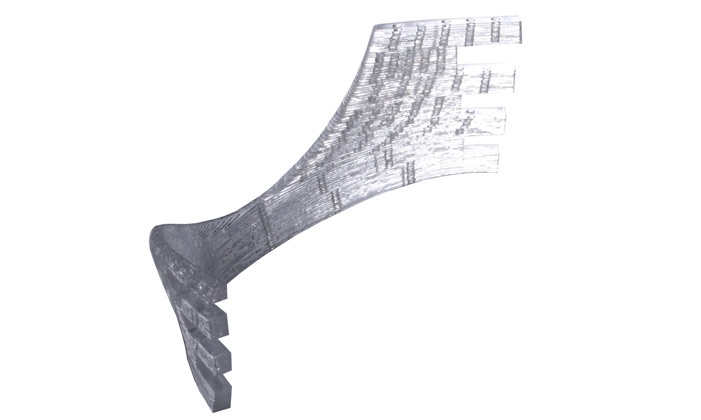
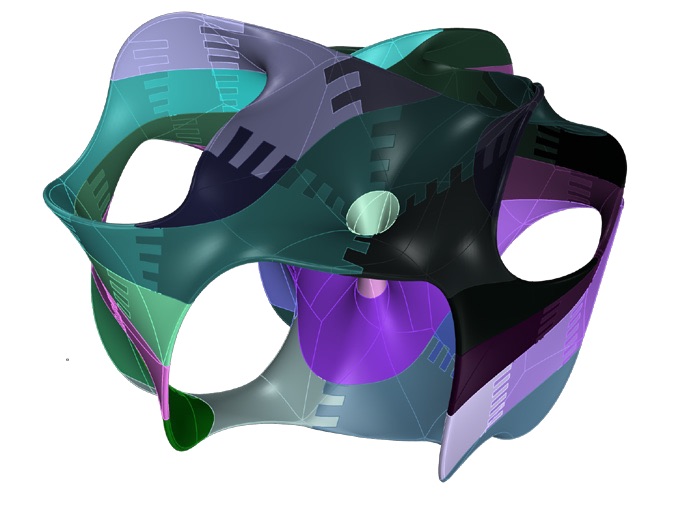
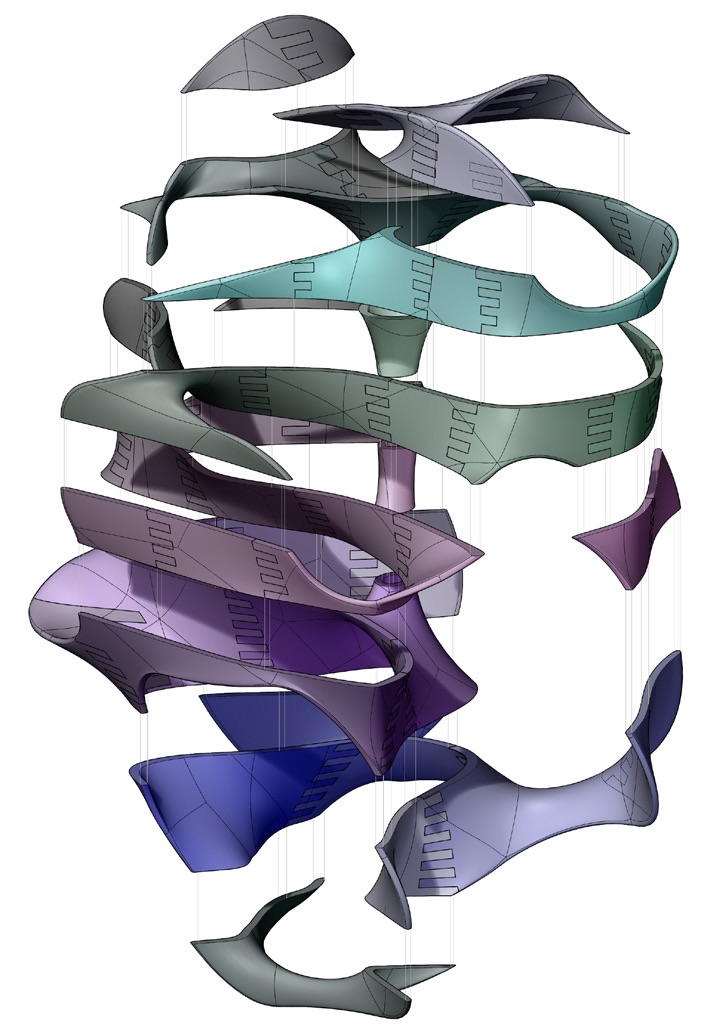
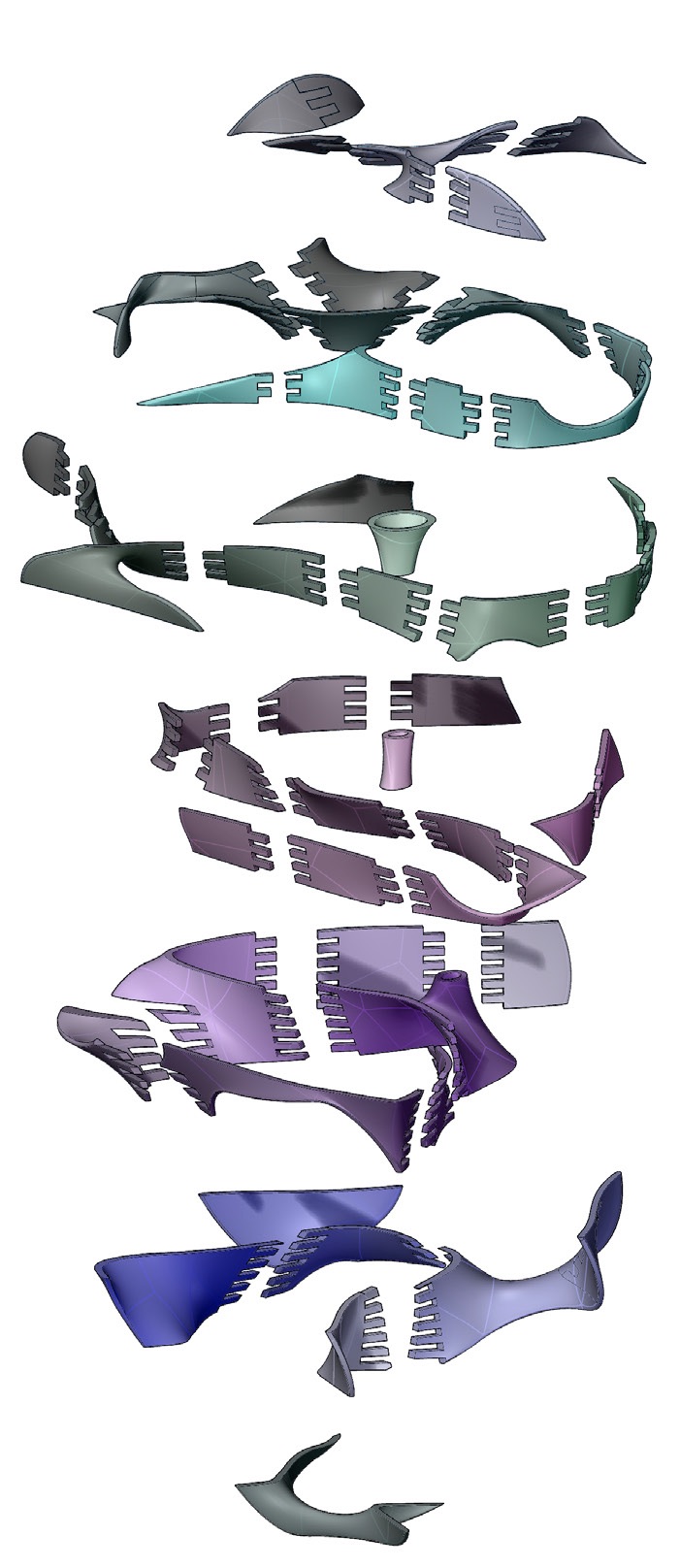
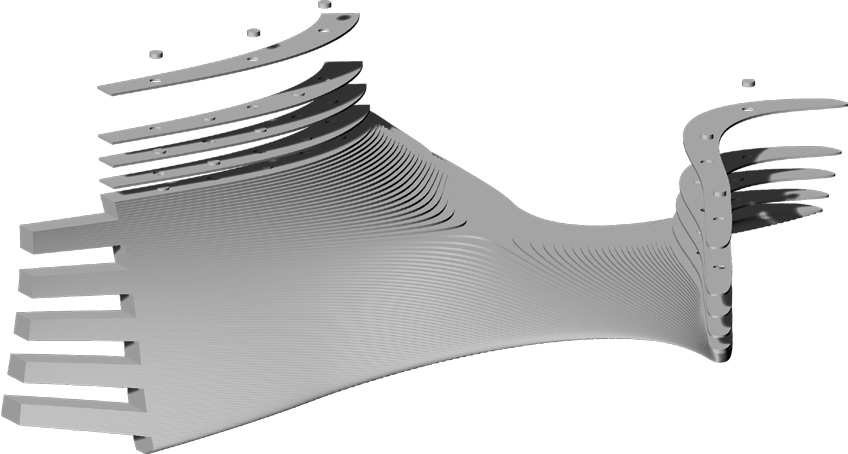
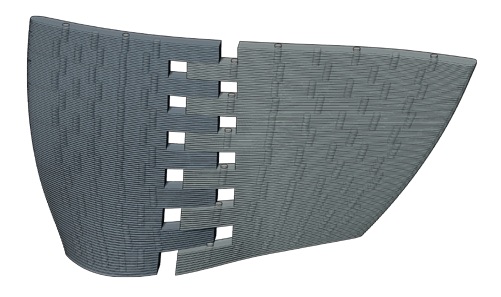
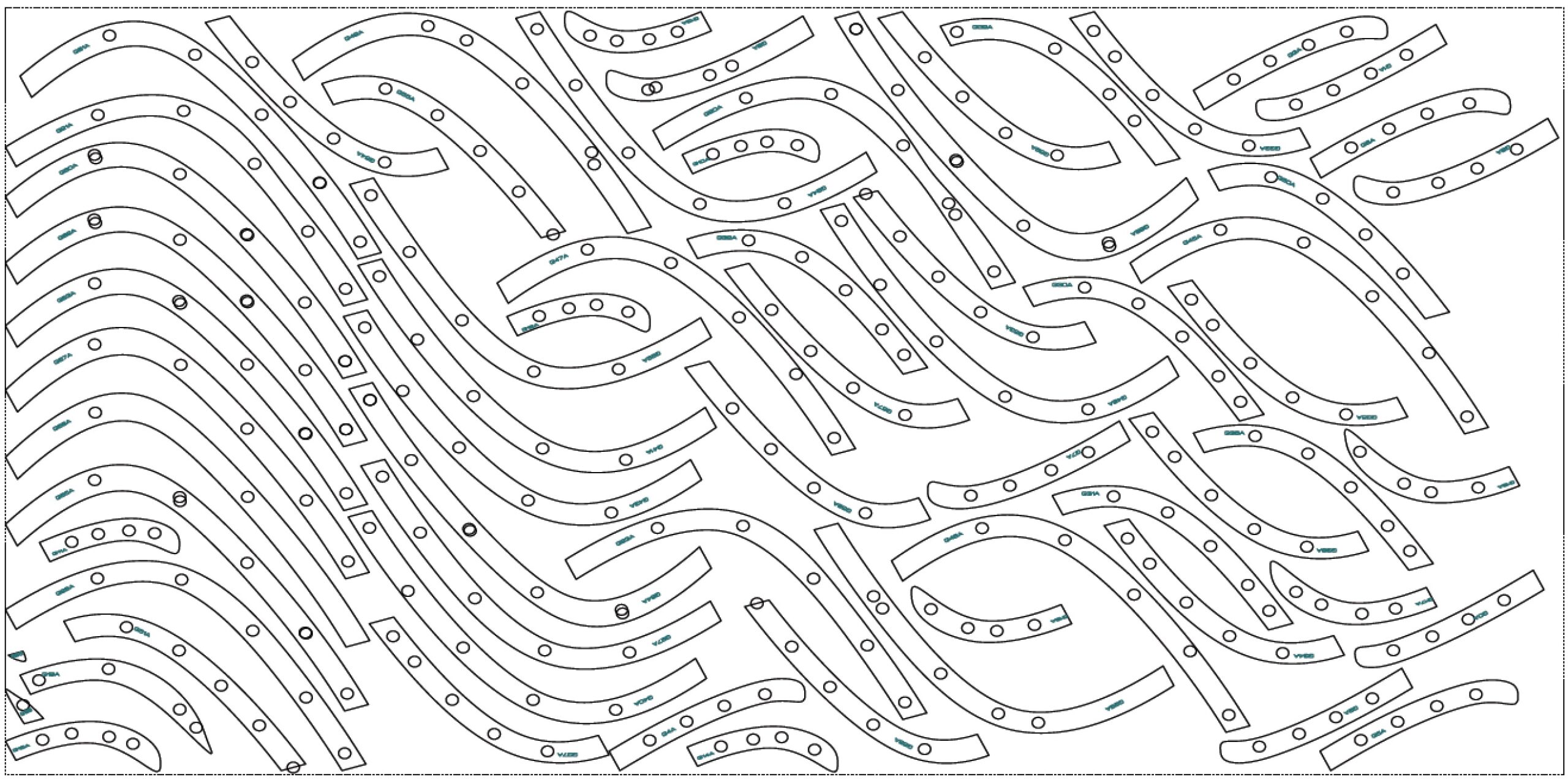
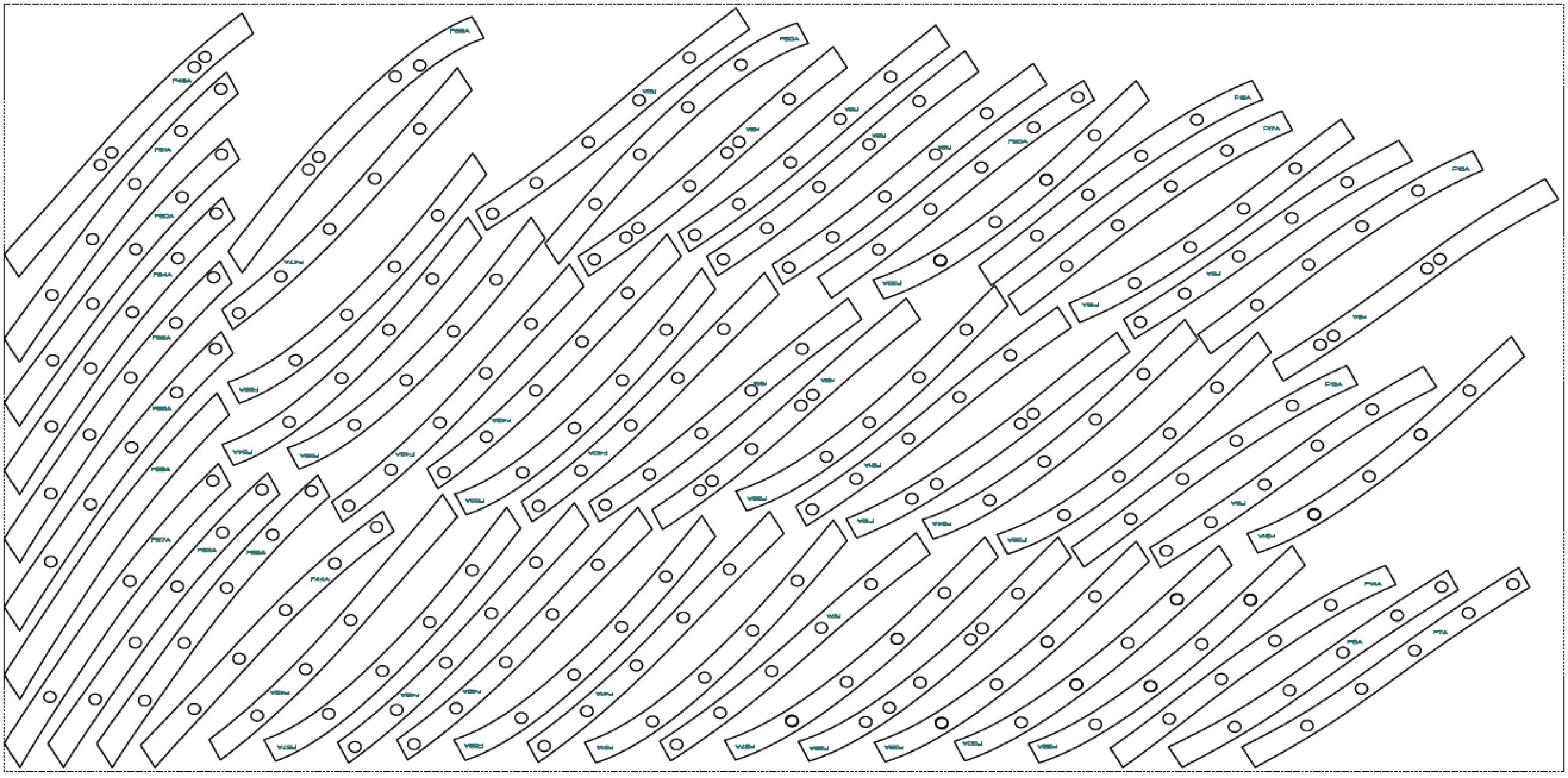
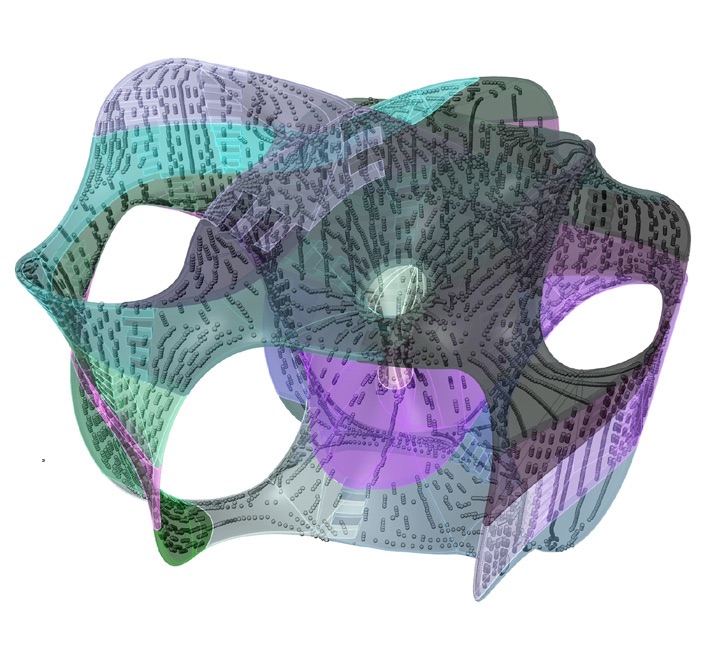
ONE-SIDED HYPER MINIMAL SURFACE (PHASE 2)
In the second phase of this project, we addressed fabrication and assembly of structure keeping in mind its outdoor location, year round temperature variation, exposure to high winds, logistics of students assembling the parts at Pratt followed by larger assembly at Milgo (3.5 miles away), and shipping of entire structure by truck to the installation site (originally in upstate New York). Towards this goal, we built an accurate scaled-up model in 1/16″ laminated plexi sheets which were laser-cut into 5,162 strips and assembled into 52 components that fit like a jig-saw puzzle. Our model was at quarter-scale which worked well since the final material alucobond is 1/4in thick. Positioning pegs, 1/8in dia, 1/8in thick, were inserted in the plexi strips to fabricate the components for accurate assembly. The images on the left page show the assembly-in-progress (left column) and five jigsaw components (right column).
The entire structure (a, this page) comprises multiple layers (b) at an angle perpendicular to the column. This inclination retains the structural integrity of the singular columnar element, the key internal structural feature of the surface. Each layer is broken down into small sub-assembly components, the 52 jig-saw pieces (c). These are joined by interlocking “finger” joints to build each layer which is stacked on others for full assembly. The sub-assembly using pegs (d,e) provides and interesting challenge of patterning their distribution. The shapes of some plexi strips can be seen in the laser-cut layout (f). The size of jigsaw components is determined by their weight based on what one or two students can carry, both during assembly of layers and while loading the truck for shipment to the factory. The structural parts at the base, and at neck regions of the surface, are larger (and heavier) for reasons of structural integrity and will require special handling.
Fabricating over 5,162 different plexi parts (not including 11,916 positioning pegs) posed a logistics challenge of organizing the production and assembly process so each individual part can be tracked, sorted, missing parts identified and defective parts re-made and replaced in the correct location. This required a systematic indexing of these parts for sequential production and systematic assembly.
Structural engineering support (finite element analysis, structural details) is being provided by LERA+, the R&D department of Leslie E. Robertson Associates, NYC.
At the time of this writing, the full-scale tests are under way. Alucobond strips are being water-jet cut at the Milgo factory, and we are beginning full-scale fabrication and assembly tests. We are grateful to our industry partners Milgo-Bufkin and LERA for their support.
Faculty: Haresh Lalvani
Students: (1-8) Kalliope Economou, Mari Kroin, Sebastian Lopez, Sharvari Mhatre, Anna Oldakowski, Brandon Spinosa, Gabe Yi (9-16) Elizabeth Austin, Ariana Cohn, Dina Elfaham, Haven Gordon, Anna Oldakowski, Arie Salomon